At 4 Summit, we’re proud to be at the forefront of a digital transformation in the steel industry. With offices in London and Sheffield, we offer a comprehensive 360 service that includes design, fabrication, supply, and installation. By embracing digitalisation and automation across our entire process, we’re setting new standards for precision, efficiency, and client satisfaction.
The Digital Advantage in Our Design Process
At the heart of our innovation is our use of Advanced Steel/Tekla, a state-of-the-art structural steel detailing software. This technology allows us to create precise 3D models and fabrication drawings with millimetre accuracy. The result? A dramatic reduction in human error and a significant boost in efficiency for our clients, from the initial design phase right through to installation.
For projects involving older or irregularly constructed buildings – a common challenge in London – we employ 3D scanning technology. This allows us to import exact measurements into our detailing software, ensuring perfect fits even in the most challenging environments, which is crucial for smooth installations.
Our CNC Machine: A Game-Changer in Fabrication
The introduction of our Computer Numerical Control (CNC) machinery has revolutionized our operations, enhancing our ability to deliver precisely fabricated steel ready for efficient installation. Here’s how:
- Precision Cutting: Our CNC machine produces 100% accurate plates directly from our detailing software, eliminating manual errors and ensuring smooth on-site assembly.
- Increased Efficiency: With the CNC handling plate production, our fabricators can focus on welding and preparing steel for installation, significantly boosting our output.
- Waste Reduction: Our ability to bundle jobs together means less material waste.
- Versatility: Our CNC can efficiently handle plates up to 30mm thick, expanding our capabilities for diverse installation projects.
Real-World Impact
We’ve seen the benefits of this digital integration across various project types, from fabrication to final installation:
– Large-Scale Projects: Custom connections are now as efficient for us to produce as typical connections, thanks to our on-demand plate cutting. This flexibility is crucial for complex installation scenarios.
– Staircases: We now can cut plate stringers in house with perfect angles and tight tolerances, ensuring superior quality, easier installation and quick turnaround.
– Supply-Only Jobs: We offer quick turnaround times for plasma-cut plates, independent of external suppliers, benefiting clients who handle their own installations.
A Streamlined Process for Our Clients
One of our key strengths has always been our full 360 service, encompassing in-house design, fabrication, and installation capabilities. This integration is a cornerstone of our operations, allowing us to offer a seamless process that consistently meets lead times. By overseeing every aspect of a project, from initial design to final installation, we maintain greater control over project timelines, reducing the risk of delays and improving overall client satisfaction.
Our longstanding commitment to keeping these crucial processes in-house sets us apart in the industry. It means we can respond quickly to client needs, make real-time adjustments, and ensure the highest quality at every stage of a project, including installation. This end-to-end control has been, and continues to be, a significant advantage for our clients.
The addition of our CNC machine has further enhanced our in-house capabilities, allowing us to be even more responsive and efficient in preparing steel for installation. It complements our existing strengths, enabling us to take on more complex projects and deliver them with even greater precision and speed, from fabrication through to final assembly on site.
Looking to the Future
As we look ahead, we’re poised to capitalise on further advancements in detailing software and fabrication technology. However, we maintain a pragmatic approach, balancing cutting-edge technology with cost-effectiveness to ensure we deliver value to our clients while maintaining our profitability. This forward-thinking approach extends to our installation services, where we continuously seek ways to improve efficiency and quality.
Conclusion
In an industry where precision and efficiency are paramount, we at 4 Summit are proving that embracing digital innovation across our full service offering is not just about keeping up – it’s about leading the way. By integrating advanced software, CNC technology, and 3D scanning into our operations, we’re not just fabricating steel; we’re forging the future of the industry, from design to installation.
If you’re looking for a steel fabricator that combines traditional craftsmanship with cutting-edge technology, and offers a complete service from design to installation, we’re ready to deliver solutions that are as forward-thinking as they are reliable. Get in touch with us today to discuss how we can bring your steel projects to life with precision, efficiency, and innovation at every stage.
Related posts
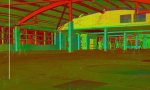
3D Scanning: Revolutionising Steel Construction Surveys
[ READ ARTICLE ]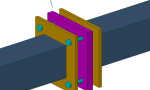
Enhancing Steel Construction: The Critical Role of Thermal Breaks
[ READ ARTICLE ]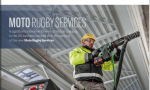
4 Summit in premier construction magazine
[ READ ARTICLE ]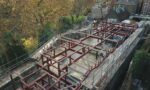
Why Is Steel Used In Construction?
[ READ ARTICLE ]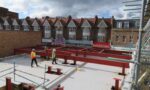
What Is Steelwork Used For?
[ READ ARTICLE ]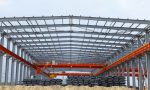
Precision grinding is used for materials.
[ READ ARTICLE ]